Printing is a complex process that involves multiple components working together to produce high-quality prints. One such critical component is the dampening roller. Understanding the role of dampening rollers and their importance in achieving consistent print results can greatly enhance your printing processes. In this blog, we will explore what dampening rollers are, how they function, and why they are indispensable in the world of printing.
ADDITIONALLY : Enhance your printing quality today by investing in high-performance Dampening rollers. Click here to explore our range of premium dampening rollers designed to deliver superior print results and ensure the longevity of your printing equipment. Don’t settle for less—upgrade your dampening rollers now!
Understanding Dampening Rollers
Dampening rollers are an integral part of the printing press, specifically in the offset printing process. Offset printing is widely used for producing high-volume prints with superior quality. In this method, the ink is not applied directly to the paper. Instead, it is first transferred to a rubber blanket, which then prints the image onto the paper. Dampening rollers play a crucial role in this process by maintaining the right balance of water and ink on the printing plate.
The primary function of dampening rollers is to deliver a consistent and controlled amount of dampening solution (a mixture of water and chemicals) to the printing plate. This dampening solution helps to keep the non-image areas of the plate moistened, preventing ink from adhering to these areas. Without the proper functioning of dampening rollers, the ink can spread to areas where it is not desired, leading to poor print quality and wasted materials.
How Dampening Rollers Work
To fully appreciate the importance of dampening rollers, it is essential to understand how they work. The dampening system consists of several rollers, including the fountain roller, ductor roller, and distributor rollers, in addition to the dampening roller itself. Each of these rollers has a specific function that contributes to the overall dampening process.
The fountain roller picks up the dampening solution from the fountain tray and transfers it to the ductor roller. The ductor roller then passes the solution to the distributor rollers, which evenly distribute it across the surface of the dampening roller. Finally, the dampening roller applies the solution to the printing plate. The even distribution of the dampening solution ensures that the non-image areas of the plate remain moist and free of ink.
This process is continuous and must be precisely controlled to maintain the quality of the print. Any variation in the amount of dampening solution can result in inconsistent print quality. Therefore, the dampening rollers must be regularly maintained and calibrated to ensure optimal performance.
Importance of Dampening Rollers for Print Quality
The quality of the final printed product is heavily influenced by the performance of the dampening rollers. There are several key reasons why dampening rollers are crucial for consistent print results:
Preventing Ink Spread
One of the primary functions of dampening rollers is to prevent ink from spreading to non-image areas of the printing plate. By keeping these areas moistened, the dampening solution ensures that ink only adheres to the image areas, resulting in sharp and clear prints. Without the proper functioning of dampening rollers, ink can spread uncontrollably, leading to blurred images and text.
Enhancing Ink Adhesion
Dampening rollers also play a significant role in enhancing ink adhesion to the image areas of the plate. The dampening solution creates a thin film of water that helps the ink to stick better to the plate. This improved adhesion results in more vibrant and accurate colors, enhancing the overall quality of the print.
Reducing Waste and Costs
Consistent print results mean fewer reprints and less waste. By maintaining the correct balance of water and ink, dampening rollers help to minimize errors and reduce the amount of wasted paper and ink. This not only improves efficiency but also helps to lower production costs, making the printing process more cost-effective.
Extending Plate Life
The dampening solution also helps to protect the printing plate from wear and tear. By keeping the plate moistened, the solution reduces friction between the plate and the rollers, thereby extending the life of the plate. This leads to longer production runs and reduces the frequency of plate replacements, contributing to overall cost savings.
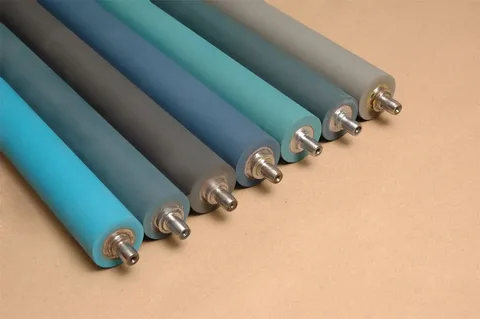
Maintenance and Care of Dampening Rollers
To ensure that dampening rollers continue to perform optimally, regular maintenance and care are essential. Proper maintenance involves cleaning the rollers to remove any build-up of ink and dampening solution, checking for wear and tear, and making necessary adjustments to ensure even distribution of the dampening solution.
Cleaning
Regular cleaning of dampening rollers is crucial to prevent the build-up of ink and other residues that can affect their performance. Cleaning should be done using appropriate cleaning agents and tools to avoid damaging the rollers. It is also important to follow the manufacturer’s recommendations for cleaning and maintenance to ensure the longevity of the rollers.
Inspection
Periodic inspection of dampening rollers is necessary to identify any signs of wear and tear. This includes checking for cracks, grooves, or other damages that can impact the even distribution of the dampening solution. Any damaged rollers should be repaired or replaced promptly to maintain print quality.
Calibration
Calibrating the dampening system involves adjusting the settings to ensure that the correct amount of dampening solution is applied to the plate. This may involve fine-tuning the pressure between the rollers, adjusting the speed of the rollers, and ensuring that the dampening solution is properly mixed. Regular calibration helps to maintain consistent print quality and reduces the risk of errors.
Innovations in Dampening Roller Technology
Advancements in printing technology have led to significant improvements in the design and functionality of dampening rollers. Modern dampening systems are more efficient, providing better control over the dampening process and enhancing print quality.
Advanced Materials
New materials are being used to manufacture dampening rollers that offer better durability and performance. These materials are designed to withstand the rigors of the printing process and provide a more consistent application of the dampening solution. Improved materials also reduce the need for frequent replacements, contributing to lower maintenance costs.
Automated Systems
Automated dampening systems are now available that provide precise control over the dampening process. These systems use sensors and computer controls to monitor and adjust the amount of dampening solution applied to the plate. Automation ensures greater accuracy and consistency, resulting in higher print quality and reduced waste.
Environmentally Friendly Solutions
There is also a growing trend towards using environmentally friendly dampening solutions that are less harmful to the environment. These solutions are designed to provide the same level of performance while reducing the environmental impact of the printing process. Using eco-friendly dampening solutions can help printing companies meet sustainability goals and reduce their carbon footprint.
Conclusion
Dampening rollers are a critical component of the offset printing process, playing a vital role in achieving consistent and high-quality print results. By maintaining the right balance of water and ink on the printing plate, dampening rollers prevent ink spread, enhance ink adhesion, reduce waste, and extend the life of printing plates. Proper maintenance and care of dampening rollers are essential to ensure their optimal performance. Innovations in dampening roller technology continue to improve the efficiency and effectiveness of the printing process, contributing to better print quality and reduced environmental impact. Understanding the importance of dampening rollers can help printing companies optimize their processes and achieve superior print results.
For more insightful articles related to this topic, feel free to visit blogsact